
The manufacturing process of self-sealing bags involves numerous steps that ensure high-quality, durable, and user-friendly products. From raw material selection to packaging and distribution, let's explore each stage in detail.
Raw Material Selection
Choosing the Right Polymers
The journey starts with selecting the appropriate polymers. Polyethylene (PE) is commonly used due to its flexibility and strength. Other polymers like polypropylene (PP) may also be utilized depending on specific requirements. The criteria for selecting high-quality polymers include tensile strength, flexibility, durability, and environmental impact.
Additives and Enhancements
To enhance the functionality of self-sealing bags, various additives are incorporated. Common additives include plasticizers for flexibility, stabilizers for durability, and UV inhibitors for protection against sunlight. Environmental considerations, such as using biodegradable or recyclable materials, play an important role in material selection.
Design and Prototyping
Initial Design Concepts
The design phase focuses on the basic structure of self-sealing bags. User-friendliness is key, so designs typically feature easy-to-use sealing mechanisms and ergonomic shapes. Ensuring the bag serves its intended purpose effectively is paramount.
Prototyping and Testing
After creating initial designs, prototypes are made to test functionality. These prototypes undergo rigorous testing to identify potential flaws and areas for improvement. Feedback leads to iterative design refinements, ensuring optimal performance before mass production begins.
Extrusion Process
Extrusion Techniques
The extrusion process melts and forms polymers into thin sheets or films. Blown film extrusion is often used, where molten polymer is formed into a tube and inflated to produce a large bubble, creating uniform, thin layers.
Temperature and Pressure Controls
Maintaining optimal temperature and pressure conditions during extrusion is crucial. Incorrect settings can lead to defects, affecting material properties and overall bag quality. Precision monitoring ensures consistency and reliability.
Sealing Mechanisms
Types of Sealing Mechanisms
Sealing mechanisms include zipper seals and adhesive seals. Zipper seals offer reusability and stronger closures but may cost more to produce. Adhesive seals are simpler but often single-use and less durable. Choosing the right type depends on the intended application.
Integration into Bag Design
During manufacturing, sealing mechanisms are integrated seamlessly into the bag. This step requires precision engineering to ensure reliable performance and ease of use. A well-designed seal enhances user satisfaction and product effectiveness.
Printing and Customization
Printing Technologies
Adding logos and designs enhances the appeal of self-sealing bags. Flexographic and digital printing techniques provide high-quality results. Ensuring print durability and clarity prevents fading and maintains brand visibility.
Customization Options
Customization options vary widely, including different sizes, colors, and additional features like tear notches or hang holes. Market trends show growing demand for personalized, visually appealing packaging.
Cutting and Shaping
Precision Cutting Techniques
Machineries such as die cutters and laser cutters are employed for precise cutting. Consistency in dimensions across batches is essential for maintaining product standards and customer satisfaction.
Shaping and Forming
Post-cutting, bags are shaped and formed to desired specifications. Methods like heat forming ensure uniformity, giving the bags their final functional shape ready for consumer use.
Quality Control
Inspection Protocols
Quality control measures involve multiple inspection stages. Incoming raw materials, intermediary products, and finished goods are thoroughly checked. Common defects like improper seals or size variances are identified and corrected promptly.
Compliance and Standards
Adherence to industry standards and regulations is mandatory. Complying with environmental and safety norms ensures both product safety and sustainability, enhancing brand reputation.
Packaging and Distribution
Final Packaging
Once manufactured, self-sealing bags are packaged for distribution. Protective packaging methods prevent damage during transit, preserving product integrity until it reaches consumers.
Logistics and Supply Chain
Effective logistics and supply chain strategies ensure timely delivery. Reliable distribution channels help maintain steady stock levels for retailers, thereby meeting market demand without delays.
Innovations and Future Trends
Technological Advancements
Recent innovations in manufacturing have improved efficiency and quality. Automation and advanced machinery reduce errors and increase production speed. Technological progress continues to drive enhancements in the field.
Sustainability Trends
Eco-friendly materials and sustainable processes are increasingly prioritized. Biodegradable plastics and recycling initiatives align with global sustainability goals, shaping the future direction of the industry.
Consumer Applications and Benefits
Everyday Uses
Self-sealing bags find widespread use in households for storing food, organizing items, and protecting valuables. Their convenience and ability to preserve contents make them indispensable for daily life.
Specialized Uses
Beyond household applications, these bags serve industrial and commercial sectors by providing secure storage solutions. They are particularly beneficial in arenas like medical supplies, electronics, and specialized packaging.
FAQs and Expert Insights
Frequently Asked Questions
Common queries about self-sealing bags often involve choosing the right type, understanding their benefits, and proper usage tips. Addressing these questions helps consumers make informed decisions.
Industry Expert Opinions
Insights from professionals in the field shed light on current trends and future projections. Experts anticipate continued advancements and greater emphasis on sustainability in self-sealing bag technology.
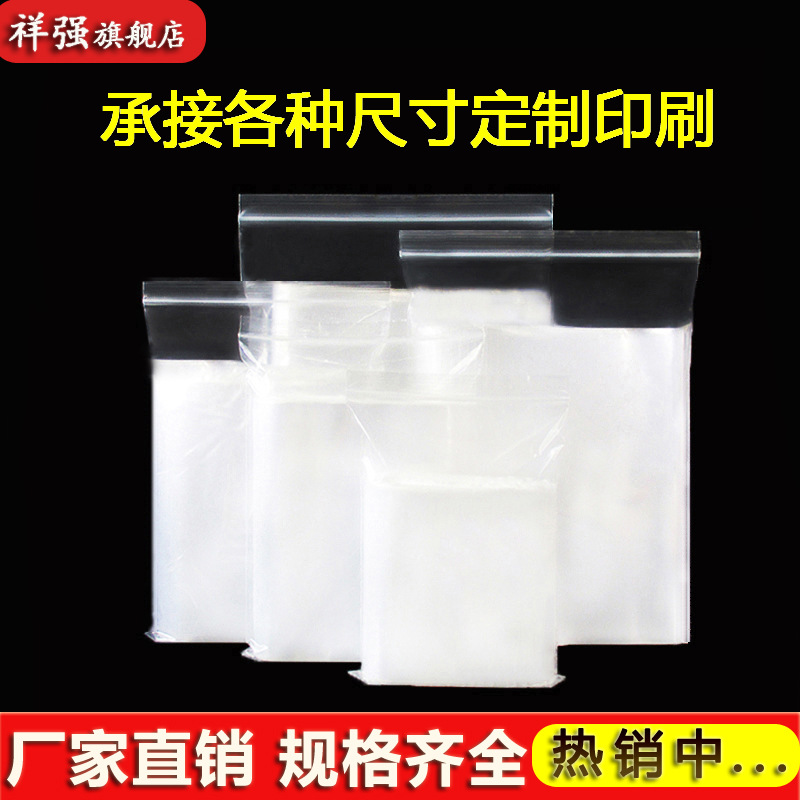
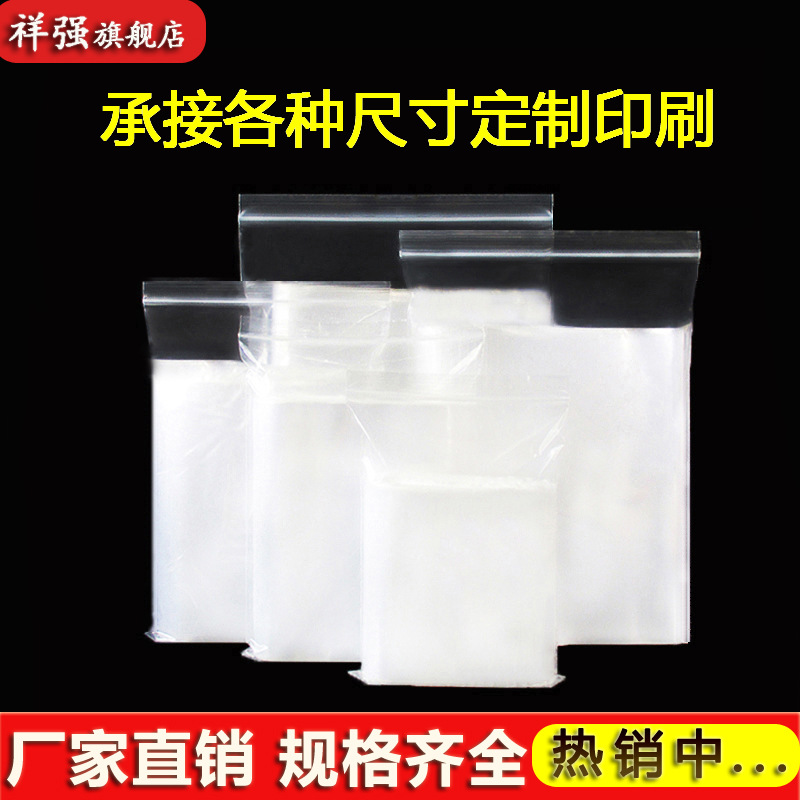